Tayto Food Production Projects
Tayto Food Production Projects: Scope of Works
Interkey Contracting was appointed to deliver a series of specialist refurbishments and operational upgrades within a live food production environment for a leading UK crisps manufacturer. With stringent hygiene regulations, tight production schedules, and zero tolerance for disruption, our team coordinated phased works alongside plant operations — ensuring full compliance with food-grade standards and minimum impact on output.
Key Project Aspects:
-
Cook Room Resurfacing: We carried out the removal of the existing floor system and installed a high-performance, food-grade resin floor finish with integral coving. The selected system was designed for thermal resistance, non-slip properties, and chemical resilience — ideal for the high-temperature, high-moisture environment of a crisp production cook room. All works were scheduled to accommodate production windows and deep-clean intervals.
-
Glass Offices Installation: To support site management and operational oversight, we delivered the design and build of modern glazed offices within the production facility. These spaces incorporated double-glazed partitions, hygienic ceiling panels, and integrated HVAC systems to maintain cleanroom-compatible airflow while improving visibility and collaboration between teams.
-
Refurbished Bathrooms: A complete strip-out and refurbishment of welfare facilities was undertaken, including installation of hygienic IPS panelling, anti-slip flooring, sensor-activated sanitaryware, and mechanical ventilation systems to comply with WRAS and DDA regulations. All finishes were selected for durability and ease of cleaning in high-usage areas.
-
Pipework, Gantry and Flues: Our mechanical and structural engineering teams designed, fabricated, and installed a robust support gantry system to accommodate new steam and extraction pipework and stainless-steel flues. The works ensured full segregation between clean and non-clean zones, with all components conforming to ATEX and food-safe standards, as required.
-
Hygiene Wall Cladding: Installed food-grade uPVC cladding systems throughout key production and packaging zones to meet HACCP and ISO 22000 standards. The system provides a seamless, easy-clean finish resistant to both moisture and impact — significantly enhancing the hygiene integrity of the facility.
-
Production Line Movement and Placement: We coordinated the strategic relocation and reinstallation of production line equipment, including bespoke mounting brackets, reinforced slab reinforcements, and services disconnection/reconnection. The entire sequence was mapped in collaboration with the client’s engineering team to ensure zero production downtime and seamless recommissioning.
-
Loading Bay and Yard Repairs: Our civil works division undertook structural repairs and resurfacing across the external loading bay and yard areas, including concrete apron replacement, reinstatement of joint sealants, and installation of dock bumpers and wheel guides. Works were phased to maintain continual HGV and forklift access.
-
Cook Room Drainage Systems: We replaced existing drainage infrastructure within the cook room area with a new 316-grade stainless steel slot drain system, designed to withstand corrosive runoff and high volumes of waste water. The works included coordinated tie-ins to existing pipework, installation of trapped gullies, and floor falls adjusted to ensure effective drainage without compromising hygiene zones.
Client
Tayto
Total Value
£4m
Programme
36 Weeks
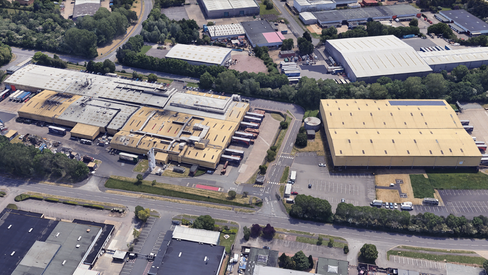
CLIENTS
CONTACT US
Enquiries
For any enquiries, questions or commendations, please call: 01536 560 550 or fill out the following form
Head Office
Office 4, Corby Enterprise Centre
London Road, NN17 5EU
Contact Us














